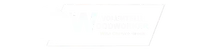
Pipe Dreams
11/1/2024 | 26m 46sVideo has Closed Captions
Host Charles Brock is joined by artistic woodworker Grant Batson.
Grant Batson is more than great at a lot of things. In his own relaxed style, he goes about life making the things that interest him most, like guitars and smoking pipes made from Italian Burr.
Volunteer Woodworker is presented by your local public television station.
Distributed nationally by American Public Television
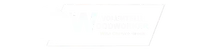
Pipe Dreams
11/1/2024 | 26m 46sVideo has Closed Captions
Grant Batson is more than great at a lot of things. In his own relaxed style, he goes about life making the things that interest him most, like guitars and smoking pipes made from Italian Burr.
How to Watch Volunteer Woodworker
Volunteer Woodworker is available to stream on pbs.org and the free PBS App, available on iPhone, Apple TV, Android TV, Android smartphones, Amazon Fire TV, Amazon Fire Tablet, Roku, Samsung Smart TV, and Vizio.
Providing Support for PBS.org
Learn Moreabout PBS online sponsorship(playful upbeat music) (logo swooshing) - Welcome to the "Volunteer Woodworker."
I'm your host, Charles Brock.
Come with me as we drive the back roads, bringing you the story of America's finest woodworkers.
(door slams) (playful upbeat music continues) We're going to Santa Fe, Tennessee to meet Grant Batson.
Grant is more than great at a lot of things.
In his own relaxed style, he goes about life making the things that interest him most, like guitars and pipes, yes, smoking pipes from Italian bur.
Let's meet Grant Batson.
- [Announcer] "Volunteer Woodworker" is funded in part by...
Since 1970, Whiteside Machine Company has been producing industrial-grade router bits in Claremont, North Carolina.
Whiteside makes carbide bits for edge-forming, grooving, and CNC application.
Learn more at whitesiderouterbits.com.
Real Milk Paint Company makes VOC-free, non-toxic milk paint available in 56 colors.
Milk Paint creates a matte wood finish that can be distressed for an antique look.
Good Wood Nashville designs custom furniture and is a supplier of vintage hardwoods.
Keri Price with Keller Williams Realty has been assisting Middle Tennessee home buyers and sellers since 2013.
Mayfield Hardwood Lumber, supplying Appalachian hardwoods worldwide.
Anna's Creative Lens.
(slow gentle guitar music) (logo swooshing) (slow gentle guitar music continues) - Grant, so nice to be here.
- Thank you for coming.
- I mean, the music and the setting, it puts me to sleep, but it doesn't- - There's a pillow right there.
Take a nap.
(Charles laughs) - I might, but I tell you what.
It doesn't do that for you.
Seems to be motivating.
Out of the many artists I know, you're so laid-back compared to most.
- My wife would disagree, but thank you.
I'll take it.
(Charles laughs) - And you're so productive.
- Hm.
- I mean, you do a little bit of everything from building a house to building a line of guitars with your brother, to building furniture, teaching, furniture-making.
And then you have a specialty like nobody else that I know that you make pipes, not just ordinary pipes, but pipes that are influenced by some of the best in the world.
- Mm-hm.
- Yeah.
- Yeah.
- So it's just amazing to be here with you.
And does the setting do something for you as an artist?
- Oh, you know, that's a great question.
I think it has to.
I don't know that I think about it a lot, but you got to walk down the path from the shop to the porch here, and it's the path that I walk every time I make pipes.
I don't typically drive down.
I walk.
And that is like a reset for me.
If I'm in a mental space...
I mean, you know, life is crazy and coming at you fast all the time, and so there's something interesting about walking down that, just, tree-covered gravel road just 250 feet or so.
Gratitude is always there.
And I feel small, and I'm surrounded by creation.
And it, I think, definitely gives me a spark that I need to be creative, so.
- What was the seed for little Grant Batson to become inspired to do all of this?
- Yeah, I mean, it's funny.
Being mindfully present and understanding these things, you really kind of have to sit in those questions.
And I have pondered these at times just as I've looked back at, how did I get here?
You know, this wasn't my plan.
And so my parents were definitely incredibly instrumental in that, as most parents impact their children in a big way.
But my mom and dad were very hardworking, and we did everything ourselves.
So I grew up in Central Texas out in the midst of corn and cotton fields.
And my dad had a little business that he ran, but we did everything ourselves.
So if a car broke down, we fixed it.
If we added onto the house, we did it ourselves.
If something needed to be welded... You know, my dad wrote a book on refrigeration.
He just did everything, including woodworking.
And so I kind of, I think the woodworking stuck out to me the most.
Oh, he's also a master electrician.
I mean, you know, he literally just, he can do all of the things.
- Was he the farmer-scientist type?
- Oh, he's very much a scientist.
Being around him is very inspirational.
I learn stuff.
We have coffee every week, and I learn things from him every time I'm with him.
He is one of my favorite people and generous to a fault and just brilliant.
So from him, I think, and my mom as well, I kind of got this attitude of if it needs to be done, you do it, and do it with the things you have.
- So there was no box.
You could always color outside the lines or inside the lines, so there was no box.
And that way, you can grow as a person and as an artist.
- Yeah, and so, you know, resourcefulness was, and it still remains a thing for me, even in furniture that I build or pipes that I make.
I a lot of times use materials that I've found (rooster crowing) or are laying around, or sometimes they're unlikely.
They're almost trash, if you will.
And I like to find a way to kind of redeem the thing that has been kicked to the side and see if I can find usefulness in it.
- Grant, from the sounds that I just heard, you're also a gentleman farmer.
- Yeah, I'm gonna go ring his neck so we can keep this conversation going.
Yeah, Joe is our rooster, and he takes care of about a dozen hens who lay eggs for us every day.
It's really my wife's passion.
(rooster continues crowing) He really wants to be in on this interview.
(Charles laughs) So, but we love it.
They're great.
The grandkids love it.
We let 'em out in the yard as long as they're not eating my wife's vegetables.
- Making pipes, you make pipes that are in a style that is known internationally, and you've learned from some great pipe makers.
- Oh, yeah.
- How did you get on that path?
- So it's kind of interesting.
I'd love to say that my life's been very intentional and that I have had a great plan, you know, but the truth is you find yourself in a situation and improvising, adapting.
It's kind of, I guess, my life story.
I think it's probably most people's story.
But pipe making for me was, it felt very much like an accident.
It was an opportunity that I stumbled on.
I was getting to the point where I needed to make a change from guitars.
And there was a pipe maker who had seen our guitar work and asked if we could build a display cabinet for some of his work.
And I was interested in it, but I'd forgotten about it.
And this was maybe a year or two before I left the guitars.
So I left the guitar business and kind of needed some work, and I remembered, "Oh, this guy's got a cabinet that needs to be built."
And so I called him up, and through the course of that time, he started teaching me pipe making, and I didn't even know that was a thing.
I thought you'd buy pipes out of a basket.
In a tobacco store, they're 20 bucks, and they're made by some machine somewhere.
But this guy's pipes were 10,000 bucks.
- Wow.
- And it blew my mind.
I had no idea.
So he starts teaching me pipe making, and I'm doing other things as well, you know.
I was building out kitchen islands in, you know, custom homes, and I built some electric guitars.
And I had a couple of other really interesting things I was working on, but nothing was really sticking.
And the guitar business had been, it had worn me out.
And so I found pipes kind of an unexpected joy.
I really thought it would be boring.
And in fact, when he told me, "Hey, you'd be really good at making pipes.
You should make pipes," and I thought...
I think I even said to him, "It looks boring."
- (laughs) Well, there is a boring part.
You've gotta bore a hole.
- That's true.
- Yes.
Or the pipe's just not gonna work, yes.
- That's right, there is some boring involved, for sure.
- (laughs) Well, what makes your pipes more than the pipe you were talking about that you saw in the tobacco shop that was probably made in assembly line?
- Well, so engineering is one of them, the way that the tobacco chamber and the airways and the fitting of things, and then, of course, materials too.
So the materials that I use, all of the pipe makers that are in the high-grade world, as we call it, they're using...
This mouthpiece material is Ebonite, which is a vulcanized rubber product that comes out from two different companies in Germany.
And then the briar is a high-quality briar that is typically coming out of Italy or Greece.
- Now, what is briar?
- So briar is the root ball of a conifer tree.
It's a conifer.
It's called the white heath.
And it's really kind of like this scrub brushy shrub that grows all over the place.
And when I say Mediterranean, it's in Algeria, Morocco, Spain, Corsica.
It's everywhere, and it just grows randomly in the foothills.
And these guys will take their wooden wheelbarrows and their pickaxes, and they'll climb up into the foothills, and they'll pick it out of the dirt.
And half of the root ball is exposed.
- So there is a briar patch.
- Very much.
- Yeah.
- Yeah, and then they'll cut these balls out and cut all the little roots off of them, and they're usually cantaloupe to watermelon in size.
And they'll roll 'em down to the edge of the road, and then a little truck comes along, and he'll buy them from them, and they'll load 'em up.
And then he'll drive them to a briar cutter, and they'll open up this big, usually it's a basement or some type of, you know, dark area in their shop.
And they'll dump that, and then they wet them down, and it's a curing process.
They'll cut them, and then they'll boil them.
They're trying to get tannins and things out of them.
But it's usually about a three-year process to get the briar from the earth and to the point where they can ship them to someone like me.
- Grant, can you take me down to the shop?
Can you show me- - Absolutely.
- How you do it?
- I would love to.
Let's do it.
- All right, let's go.
(playful upbeat music) (logo swooshing) (slow gentle guitar music) (slow gentle guitar music continues) Well, this is briar.
(logo swooshing) - Yes, sir.
- And I can see the grain.
It's tight.
- [Grant] It's very tight.
- Yeah, it's got a little heft to it too.
- It's very dense, yeah.
- What makes briar the special wood to make a pipe chamber out of?
- So, someone way older and smarter than me somehow figured out, like the mushrooms we were talking about, which ones do you eat, which ones you don't.
- Yeah.
- So somehow, somewhere, they figured out that the density, the properties of this wood, this combustible material, are actually quite ideal to light something on fire inside of and have it not burn up.
So, as it burns the tobacco, it begins to create this kind of a coating, a caked layer on the inside of what we call a tobacco chamber that insulates the rest of it from burning up.
And it's just the ideal wood.
Pipes have been made of everything, stone and cherry and pine and, you know, willow and all kinds of things.
But briar is, it's the one.
It's the chosen one.
- Well, it's got an interesting look to it.
What's this?
- Yeah.
This is the live bark edge.
We call it plateau.
This one's actually got a little bit of a rough loose-grain pattern.
So while all of them have a dense, very close grain structure, some are looser than others, and you can tell kind of by the bird's eye on the plateau.
This one's one that's got tighter... And then you, of course, I've got some that are much tighter.
If you can look at the difference, the closeness of those bird's eye- - Yeah.
- Compared to those.
And this is actually going to be a much more expensive block, and it's going to produce a much more beautifully aesthetic pipe.
- So when you look at this, how can you tell where the chamber needs to be?
- [Grant] So typically, I'm not as concerned about the location of the chamber because the makeup of this wood, it does fine wherever it is.
- I see.
- But what I'm really gonna go for is I'm gonna try to follow the pattern of the starbursting grain.
It's growing from the center out.
It's round.
I'm gonna try to follow it in either a cross grain or a lateral grain so that I can draw out the absolute beauty of it.
I don't want to really cut through the grain.
I wanna follow along with it.
So as I'm making this, I can try to have a shape in my brain about what I'm gonna make, but I find that when I sit there, the wood itself begins to tell me, "You can't do that.
You gotta go this way."
And so I'm constantly making decisions based on what the wood's telling me to do.
- So the artistry is to listen and to look.
- Yep.
- Feel.
Use your senses.
- That's right, yeah, paying attention to it.
You can make a pretty pipe.
Briar's pretty no matter what, but if you're really paying attention to it, you can draw out the absolute best of it.
And that's the challenge every time I sit down.
In fact, I've been intimidated by blocks.
I've picked up a very expensive, beautiful block, and I think, "Oh my, I've never seen one this good.
Don't mess it up," you know?
And I have messed them up, you know, so.
- Well, let's see how you do it.
- Okay, I'd love to show you.
Feel free to put the masks on.
I'm not gonna wear one.
I never do.
This dust collection does a pretty good job.
(playful upbeat music) (playful upbeat music continues) (playful upbeat music continues) So now I've kind of made some decisions about what the grain needs from me, and now I'm gonna really try to just begin to refine a shape out of it once I've exposed most of the grain.
(machine buzzing) - Wow, that's a great shape.
It really is.
Is this kind of a classic shape?
- So this would probably fall into the Dublin category.
Dublins tend to have a flared outward chamber, but it's very much a freehand style of a Dublin.
So what I like about this is having the plateau on the top, revealing the bird's eye, and then having... You'll have what's called a panel on the bottom side, and this will all be bird's eye.
But then here, if you can see the pattern of the grain, it flares out.
- Yeah, yeah.
- And I've tried to create the shape, the taper- - Wow.
- So that it perfectly exposes the lines of that- - Kind of lifts up.
- Grain structure.
- Yeah, and then do you leave a little bit of live edge?
- I do.
I like to leave live edge as often as I can, and sometimes you can't.
Sometimes it has to go away for the shape to be right.
Every time it goes away, though, I'm a little disappointed.
I like to leave live edge because this is a luxury product.
You know, I've made a lot of luxury products through time, and it's got a big price tag on it.
And for me, sometimes you lose the story.
This has a story.
This was in the dirt on the side of a mountain, and some relatively poor people with wooden wheelbarrows came through, and they pickaxed it out of the ground and rolled it down the hill.
And it, to me, it's a reminder.
Having that live edge reminds someone that this is an organic plant that came from somewhere.
And now it's been given a different purpose now, but it's got a story.
- You're celebrating that story.
- Yeah, yeah.
- Yeah, you do it beautifully.
Well, what's the next step?
- So the next step will be, I will draw four axis lines around this thing intersecting so that I can hand drill it.
Here is actually eyeballing a perfectly straight line around a very curved substrate, I guess, because if your line is off, your drilling is off.
And you can really make a bad go of this ordeal.
So, trying to really make sure that it's perfectly straight.
So I'm kind of closing one eye here, and what I'm doing is, as I rotate around, I'm kind of like interpolating.
It's funny when I'm teaching woodworking stuff in other venues, I emphasize not to skip grits.
- Right, yes.
(Grant laughs) - And then here I am going from 24 to 120.
And now we're ready to drill it out.
- [Charles] Let's do it.
- Let's do it.
So each line is very intentionally placed and has to intersect with its counterpart perfectly for the engineering that we talked about earlier to be spot on.
So the first one that we're going to drill is called the mortise, and it will need to be perpendicular to the very end of this shank, and it also needs to be straight this way.
You don't want some weird-angle mouthpiece coming out.
And the mouthpiece is a friction fit into, this is called the stumble or the body of the pipe.
And so, we'll first drill the mortise, and then we drill the airway.
And I really need that airway to be right in the center of the bottom of that mortise.
And then it needs to be in the center of the bottom of the corresponding tobacco chamber.
- To get those holes that you're gonna bore to all come together at the right place, that's a boring proposition.
(Grant chuckles) - Am I boring you?
- You're gonna be boring it.
- Okay, here we go.
Let's do it.
(machine whirring) (playful upbeat music) (playful upbeat music continues) (playful upbeat music continues) So I connected.
That's good.
- So it's not too long before this will be a pipe.
- Yeah, that's right.
So I've got a little sanding to do.
I've got some special sanding disks that I've made for this next step.
A mouthpiece I'll make.
I'll probably put some type of adornment up here, but pretty long- - It's gonna be a pipe.
- Yeah, it's gonna be a pipe.
(Charles laughs) - This has been wonderful.
- Yes, it has.
Thank you so much for coming.
- I'm gonna be heading down the road to find a story of another great woodworker.
See you next time on the "Volunteer Woodworker."
(door slams) (playful upbeat music) (playful upbeat music continues) - [Announcer] "Volunteer Woodworker" is funded in part by...
Since 1970 Whiteside Machine Company has been producing industrial-grade router bits in Claremont, North Carolina.
Whiteside makes carbide bits for edge-forming, grooving, and CNC application.
Learn more at whitesiderouterbits.com.
Real Milk Paint Company makes VOC-free, non-toxic milk paint available in 56 colors.
Milk paint creates a matte wood finish that can be distressed for an antique look.
Good Wood Nashville designs custom furniture and is a supplier of vintage hardwoods.
Keri Price with Keller Williams Realty has been assisting Middle Tennessee home buyers and sellers since 2013.
Mayfield Hardwood Lumber, supplying Appalachian hardwoods worldwide.
Anna's Creative Lens, crafters of resin-on-wood decorative arts.
Visit charlesbrockchairmaker.com for all you need to know about woodworking.
If you'd like to learn even more, free classes in a variety of subjects are available for streaming from charlesbrockchairmaker.com.
(gentle upbeat music) (upbeat music)
Volunteer Woodworker is presented by your local public television station.
Distributed nationally by American Public Television